Der hintere Teil vom Aufbau ist besonders stark von der Hitzeentwicklung rund um den Kessel betroffen. Daher habe ich in diesem Innenbereich alles mit Alu-Blech verkleidet. Nachdem die Blechteile ausgeschnitten, gebogen und angepasst waren, wurden sie mit hitzebeständigem Silikonkleber befestigt.
Kategorie: Glasgow (Graupner)
Bauberichte von dem Seiten-Schaufelrad-Dampfer Glasgow mit Hybridantrieb. A.k.a Lady Scarlett
Auseinandertreiben…
Im Original hat der Schornstein eines „Steam Paddle Tugs“ am oberen Ende eine Wölbung nach außen. Dies kann man auch im Modell, ohne teures Spezialwerkzeug, recht einfach bewerkstelligen.
Man benötigt nur einen Gummi-Hammer, ein Stück Holz und einen Trichter. Mir erschien der Trichter, welchen wir seinerzeit für die Zubereitung der Baby-Flaschen verwendet hatten, von der Neigung her optimal.
Man Stülpt das Alu-Rohr über den Trichter und schlägt dann mit dem Gummihammer, mit sanfter Gewalt auf das Stück Holz und treibt so das Aluminium auseinander. (siehe Bild)
Trichter für Baby-Flaschen Sanfte Gewalt prüfen ob gleichmäßig Fertig
Rede kein Blech, biege es !
Original wird der Aufbau komplett aus Holz gefertigt. Über den Kessel soll zwar von innen ein Hitzeschutzblech mit Lüftungsöffnungen angebracht werden aber die Heiße Luft vom Kessel staut sich trotzdem darunter. Wie man aus dem Internet weiß, ist zumindest eine Glasgow daher wohl Opfer der Flammen geworden.
Daher habe ich den Teil des Aufbaus, welcher über dem Kessel ist komplett aus Alu-Lochblech gefertigt. Eine Biegemaschine braucht man dafür nicht, ein kleiner Schraubstock und ein paar Holzreste kann man zum Biegen prima verwenden. Ich hoffe, dass über das Lochblech die Wärme besser nach außen Abtransportiert werden kann.
Die Lüfter habe ich deshalb nicht aus ABS gefertigt sondern welche aus Metall (brüniert H60mm Krick RC 61785) besorgt. Sie sind zwar etwas kürzer als die Originalen, aber das fällt kaum auf.
Einfache Biegevorrichtung Maßnehmen Passt! Original Graupner (aus Holz und ABS) Original Dampfspezi (Holz, Alu und Metall)
Darauf kann man aufbauen…
Nachdem nun Rumpf, Technik, Mechanik und das Deck soweit fertig sind, geht es an die Aufbauten. Die Holzteile wurden mittels Feile an das Deck angepasst. Der zusammen geleimte Korpus wurde nach ca. 20 Minuten Trockenzeit auf das Schiffsdeck aufgesetzt und dann während der vollständigen Trocknung mit Gewichten (Wasserflaschen) beschwert. Somit passte sich der Korpus perfekt an das Deck an.
Gewichte Klammern Klebeband Während der Trockenphase Passt!
An Deck!
Nachdem im Inneren des Rumpfes alle Vorarbeiten beendet waren, wurde das Deck eingeklebt.
Zuvor mussten noch die Rohre für die Ankerkette angefertigt werden. Diese wurden, anders als im Bauplan beschrieben, nicht aus geraden Rohren hergestellt, sondern mit dem Biegegerät passend gebogen. Zum Einkleben im Rumpf habe ich Stabilit-Express© verwendet.
Nachdem dies getrocknet war, wurde das Deck in die dafür vorgesehene Nut mit UHU-Hart© eingeklebt und die beiden Rohrenden durch die Öffnungen im Deck geführt. Der Streifen türkis an der Verschanzung der Reling wurde zuvor mit Lackierer-Klebeband abgeklebt damit dieser nicht beim Einsetzen des Decks beschädigt wurde. Gummi-Bänder wurden während der Trockenphase um den Rumpf gemacht. Jetzt geht es mit den Aufbauten weiter…
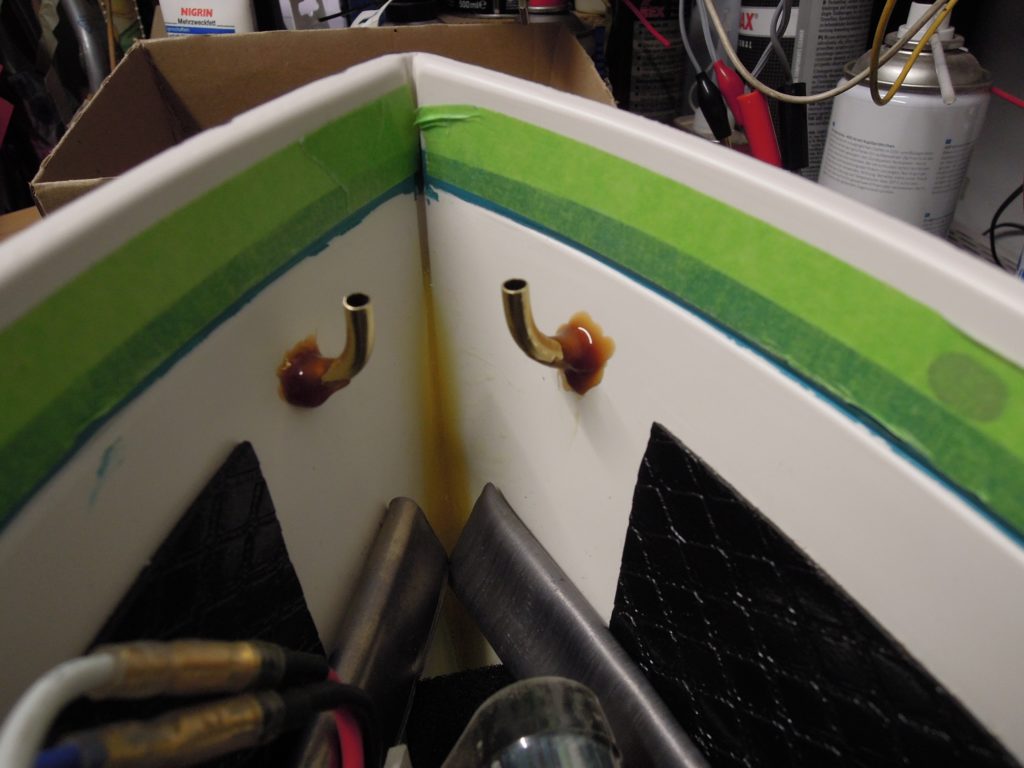
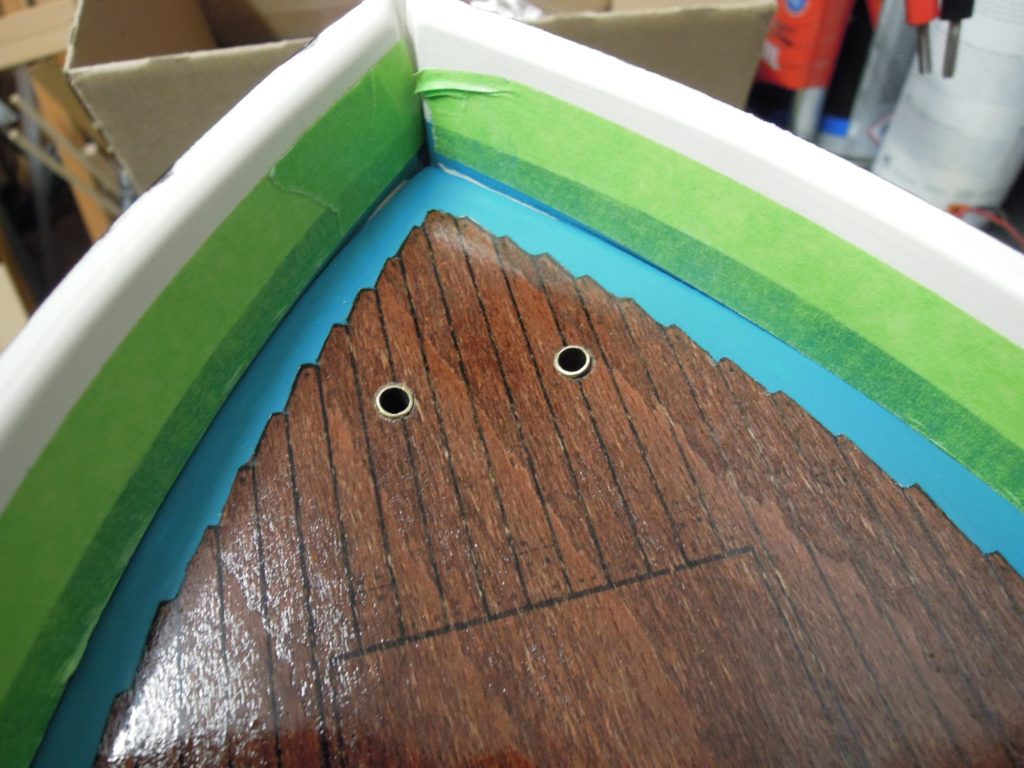
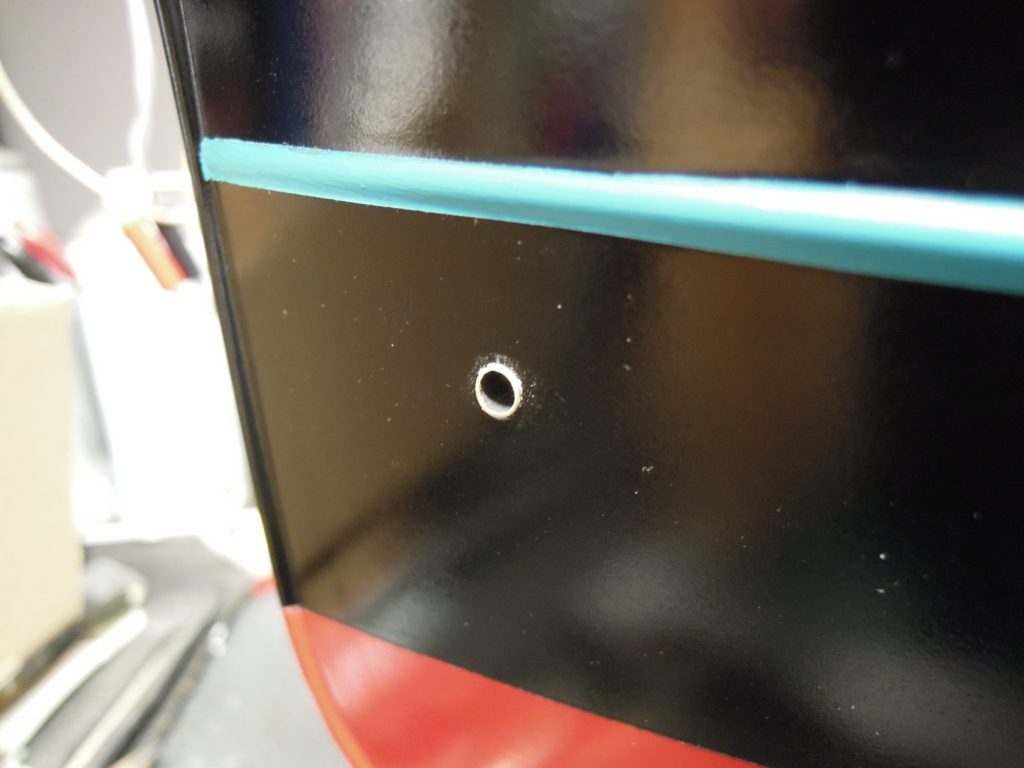
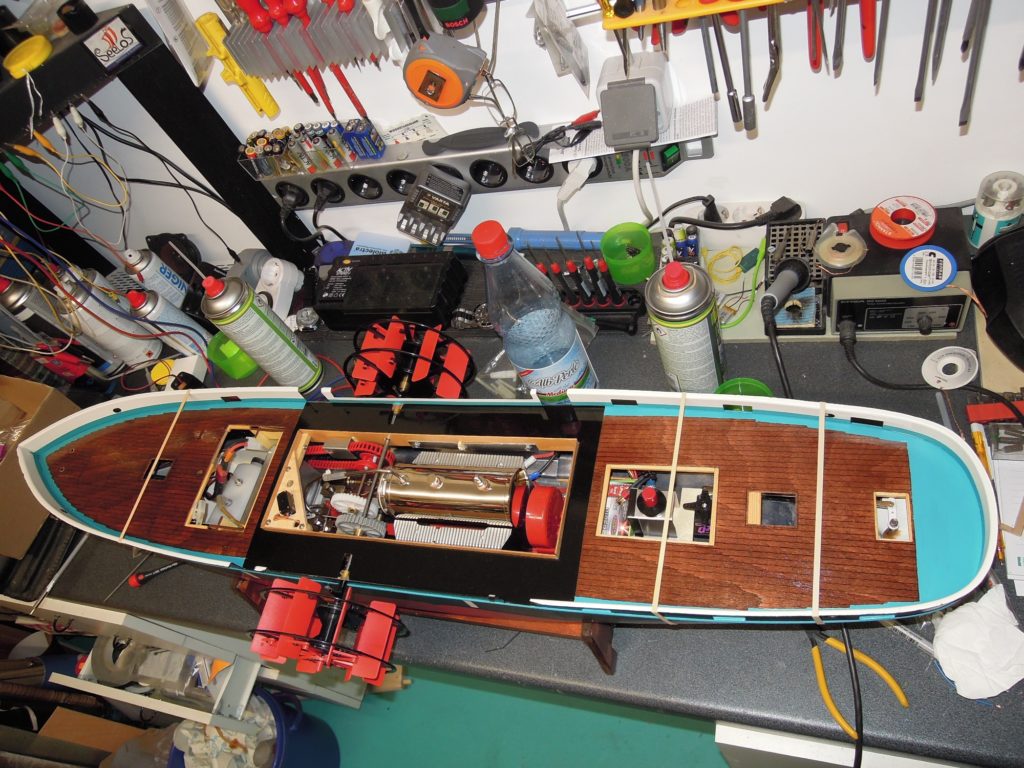
Nötiger Ballast
Nachdem Mechanik und Technik verbaut wurden liegt die Glasgow immer noch nicht tief genug im Wasser. Ein „Stapellauf“ in der heimischen Badewanne ergab, dass ca. 2,6kg zusätzliches Gewicht benötigt werden damit der Schlepper knapp oberhalb der Wasserlinie im Wasser liegt.
In der Summe ergibt das zur Zeit ein Gewicht von ca. 6,8kg. Mit Aufbauten wird das Gesamtgewicht also ungefähr bei 7kg liegen.
Ich habe mir daher vom Dachdecker 3kg Walzblei besorgt. Walzblei kann man sehr gut verarbeiten (schneiden, rollen, biegen). Da Blei giftig ist, bitte bei der Verarbeitung Handschuhe tragen und sicherheitshalber auch danach die Hände waschen! Das Blei habe ich zurecht geschnitten und über die ganze Rumpflänge verteilt. Das zusätzliche Gewicht sollte man unbedingt vor dem Einkleben des Decks platzieren, da man später nicht mehr an alle Bereiche im Rumpf heran kommt.
Wasserlinie ohne Blei Test wieviel Gewicht Zurecht schneiden Falten Blei im Bug Blei seitlich Blei Achtern Nun stimmt die Wasserlinie
Revisionsöffnung
Falls ich mal die Achse, auf der die Zahnräder sitzen, ausbauen müsste habe ich eine Revisionsöffnung im Rumpf vorgesehen. Diese Öffnung wird im normalen Betrieb mit einem kleinen Durchführung aus Gummi (aus dem Befestigungsmaterial für Servos) und einem Kunstsoff-Pfropfen verschlossen.
Gummi-Durchführung Verschlossen mit Pfropfen So kann man die Achse bei Bedarf heraus ziehen
Man weiß ja nie…
Vielleicht möchte ich ja später mal aus irgend einem Grund ein Kabel von ganz hinten nach ganz vorne ziehen? – Wahrscheinlich werde ich das nie machen, aber für den Fall der Fälle habe ich noch eine Schnur durch die Spanten gezogen. So könnte ich bei Bedarf ein Kabel daran knoten und durchziehen.
Schnur vorne Schnur hinten
Hybrid-Antrieb
Die eigentliche Umschaltung zwischen den Antriebsarten, Dampf und Elektro, war ja bereits entwickelt und getestet.
Eine ungelöste Aufgabe war bis vor kurzem die Ansteuerung der Umschaltung für die beiden Antriebsarten via Servo. Aber auch für diese Aufgabenstellung gab es eine Lösung.
Etwas Tüftelarbeit, da man den Servo ja nicht an „Lufthaken“ aufhängen kann 🙂
Kurz und gut: Jetzt funktioniert es!
Betriebsart: Elektro Betriebsart: Dampf Servo und Gestänge
Vollgestopft
Viel Platz ist nicht mehr im Rumpf.
Nach dem Lackieren durfte die Mechanik und Technik nun endlich an ihren Platz im Rumpf.
Folgendes ist nun funktionstüchtig verbaut:
– Dampfmaschine mit Gastank, Aggregat und Kondenser
– Geschwindigkeitsreglung der Dampfmaschinen per Servo
– Piezo Funkenzünder per Druckknopf (Entzünden der Brenner-Flamme)
– Kühlgebläse per PC-Lüfter
– Ruder (links/rechts) per Servo mit fast 90° Wirkung
– Failsafe für Ruder (Schiff fährt im Kreis bei Ausfall Sender)
– Antriebsartumschaltung per Servo (Dampf oder Elektro)
– Geschwindigkeitsreglung Elektroantrieb per Fahrtregler
Weitere Details folgen in den nächsten Tagen…