Nachdem im Inneren des Rumpfes alle Vorarbeiten beendet waren, wurde das Deck eingeklebt.
Zuvor mussten noch die Rohre für die Ankerkette angefertigt werden. Diese wurden, anders als im Bauplan beschrieben, nicht aus geraden Rohren hergestellt, sondern mit dem Biegegerät passend gebogen. Zum Einkleben im Rumpf habe ich Stabilit-Express© verwendet.
Nachdem dies getrocknet war, wurde das Deck in die dafür vorgesehene Nut mit UHU-Hart© eingeklebt und die beiden Rohrenden durch die Öffnungen im Deck geführt. Der Streifen türkis an der Verschanzung der Reling wurde zuvor mit Lackierer-Klebeband abgeklebt damit dieser nicht beim Einsetzen des Decks beschädigt wurde. Gummi-Bänder wurden während der Trockenphase um den Rumpf gemacht. Jetzt geht es mit den Aufbauten weiter…
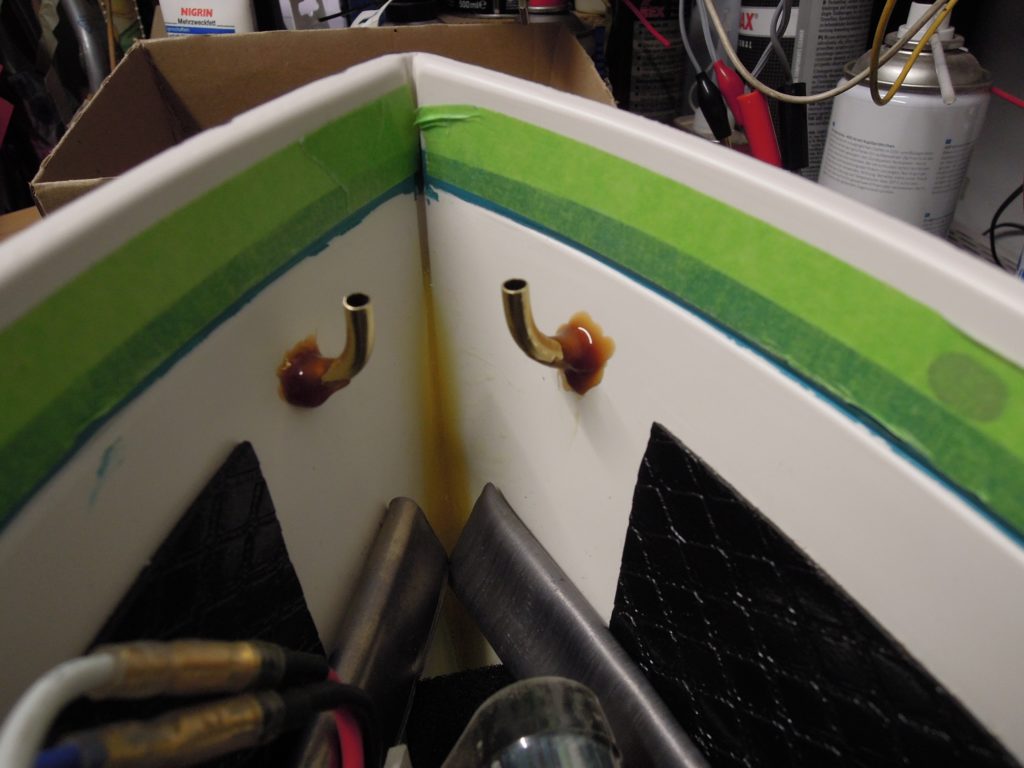
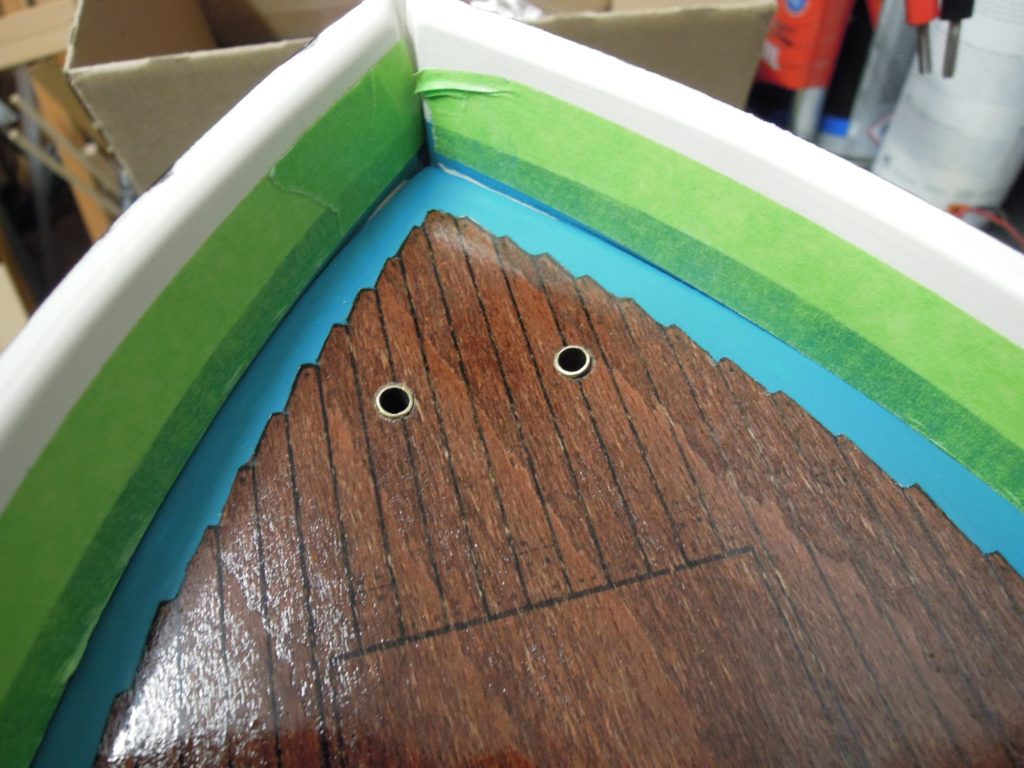
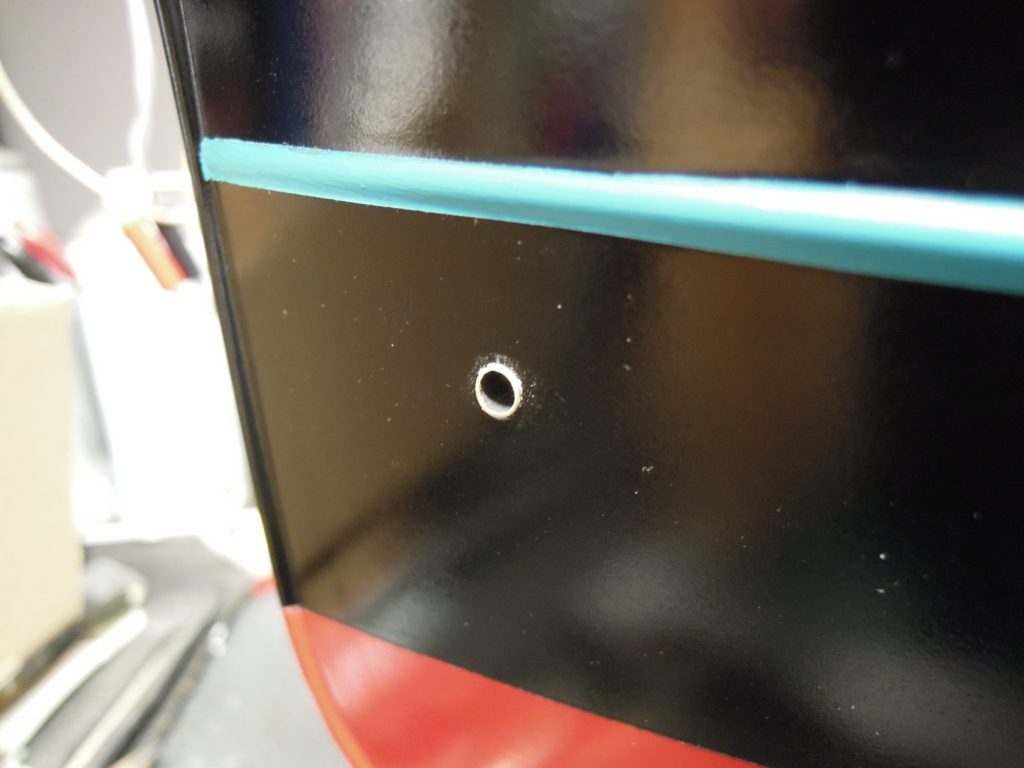
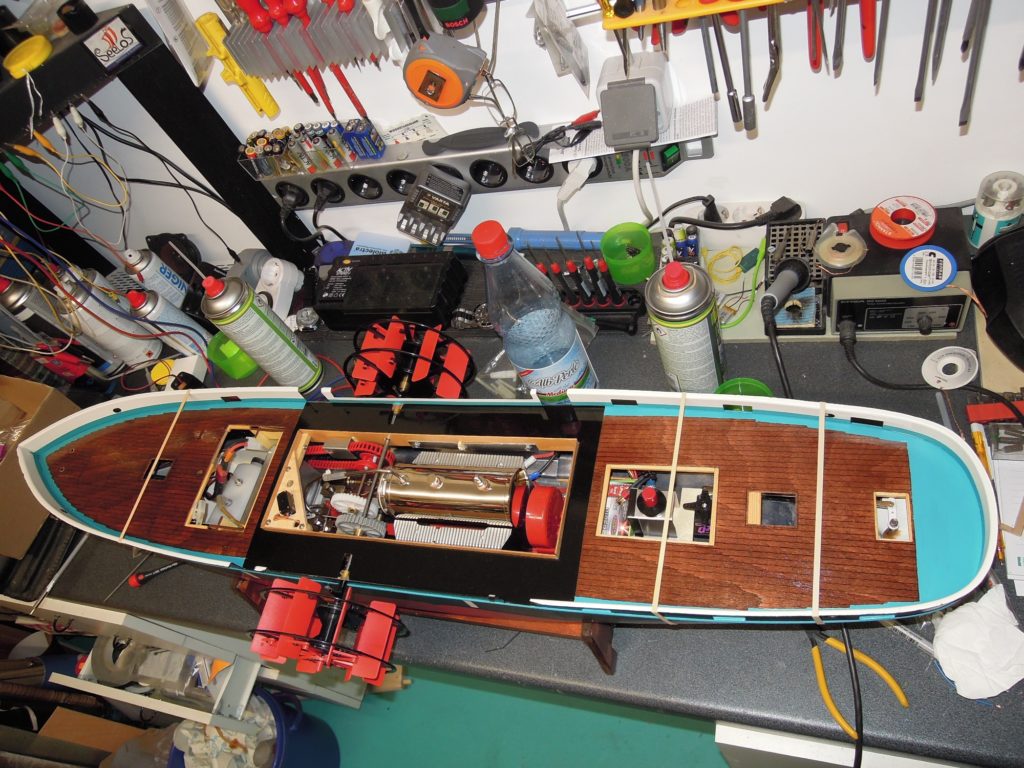